In April 2025, President Donald Trump introduced a new set of tariffs targeting critical construction materials, including steel, aluminum, and various imports from China, Mexico, and Canada. These measures have sent shockwaves through the U.S. construction industry, leading to increased costs, project delays, and heightened uncertainty. This article explores the recent tariffs’ implications for the construction sector and offers strategies to navigate these challenges.
Understanding the New Tariffs
On April 2, 2025, the Trump administration implemented a 25% tariff on all steel and aluminum imports, affecting major suppliers like Canada, Mexico, and China. Additionally, a 10% tariff was imposed on a broad range of Chinese goods, encompassing essential construction materials such as metals, coatings, plumbing components, and HVAC parts. These actions aim to bolster domestic manufacturing and address trade imbalances but have introduced significant disruptions to the construction industry.
Overview of the April 2025 Tariff Actions
- Section 232 Metals Tariffs Expanded
On March 11, 2025, Trump’s administration removed previous exemptions and raised tariffs on steel and aluminum imports to 25%, extending duties to 289 downstream steel and aluminum products—everything from nuts and bolts to bulldozer blades and stainless steel sinks—impacting nearly $147.3 billion in import value annually. - Global Reciprocal Tariffs Introduced
Building on the metals duties, on April 2 the White House announced a 10% global import tariff intended to match other countries’ rates and counteract non‑tariff barriers. While initially paused for Canada and Mexico, exclusions could be reinstated or lifted later in 2025, creating further uncertainty for North American supply chains. - New Probe into Critical Minerals
On April 15, Trump ordered a Section 232 investigation into potential tariffs on all U.S. critical mineral imports—particularly cobalt, nickel, uranium, and rare earths—citing overreliance on foreign processing capacity. The Commerce Department has 180 days to complete the review, raising questions about future duties on minerals vital to steelmaking, electronics, and energy infrastructure.
Impact on Material Costs
- Steel and Aluminum Price Surges
Futures prices for hot‑rolled steel leapt over 21%—about $166 per ton—since the tariff revisions were announced, pushing domestic steel prices back to levels last seen during the first round of Section 232 duties in 2018. Aluminum producers are similarly eyeing price hikes as 25% duties erode previous cost advantages of importers. - Lumber Duties on the Horizon
While Canadian and Mexican softwood lumber remained exempt from the April 2 tariffs, the Commerce Department is already imposing 14.5% duties on Canadian lumber with plans to raise them to 34.5% later in 2025. Given that Canada supplies roughly 85% of U.S. softwood imports, higher lumber tariffs risk adding tens of thousands of dollars to the cost of a typical home. - Broad-Based Import Tax Effects
With all building materials—from washing machines to distribution transformers—subject to higher levies, NAHB data shows imported goods account for about 7% of materials used in new single‑ and multi‑family housing, totaling $14 billion in 2024. Any tariff increase on these goods directly translates to higher home prices and reduced affordability.
Residential Construction: A Steeper Climb
- Per‑Home Cost Increases
According to the NAHB/Wells Fargo Housing Market Index, builders estimated that the 2025 tariff actions alone were adding about $9,200 to the cost of an average single‑family home—before accounting for the lumber duties set to climb later this year. - Affordability Hits First‑Time Buyers
With overall material costs up 34% since December 2020—far outpacing general inflation—first‑time and lower‑income homebuyers are being squeezed out of the market. Higher mortgage rates combined with construction cost surges threaten to stall the country’s already‑strained housing supply. - Developer Slowdowns and Cancellations
Fixed‑price contracts signed before the tariff announcements are now loss‑making for builders, prompting some developers to delay or cancel projects until there’s more clarity on costs. Even when projects proceed, contingency budgets must swell to 7–10% to absorb unforeseen tariff spikes.
Commercial and Infrastructure Projects: Pinched Budgets
- Steel‑Intensive Projects Under Strain
Office towers, warehouses, and hospitals—all heavy users of structural steel—face steep budget increases. Equipment makers report they may pass along 8–10% higher input costs to customers because setting up new U.S. capacity for small, machined steel components is financially unviable compared to paying the 25% tariff. - Clean Energy Sector Impact
Recent steel and aluminum tariff hikes, along with the new 10% global duty, are projected to raise wind and solar project costs by roughly 1%, translating to as much as $53 billion in additional annual tariff expenses for the energy industry. Transmission lines, transformers, and turbine components are all affected, potentially slowing America’s clean energy transition. - Transportation and Heavy Equipment
Tariffs on bulldozer blades, hydraulic components, and tractor parts are driving machinery costs higher. Some equipment manufacturers warn that even a 25% duty is still cheaper than reshoring labor‑intensive component production, but these costs inevitably pass through to end users, from farmers to construction firms.
Supply Chain Disruptions and Delays
- Exemption Expirations
The March 12 metals tariffs eliminated most previous exemptions for Canada and Mexico. While some duties were paused or narrowed, the long‑term removal of exemptions has suppliers scrambling to find tariff‑free or lower‑tariff sources—often with longer lead times and higher freight costs. - Nearshoring and Alternative Sourcing
To mitigate disruption, many firms are exploring nearshoring options in Latin America and Southeast Asia, or increasing domestic purchases where possible. Bulk‑buy strategies—ordering steel, aluminum, and lumber before further tariff hikes—are common, but require large upfront capital outlays. - Extended Project Timelines
Uncertainty around final material costs has stretched the planning phase of nonresidential projects by weeks or months. Builders must continually update budgets and bids to reflect the latest tariff news, slowing approvals and extending overall timelines.
Broader Economic Implications
- Inflationary Pressures
Tariff‑driven material cost increases feed into general inflation, reducing consumers’ purchasing power and eroding real wages—especially for lower‑income households that spend a higher share of income on housing. - Investment Hesitation
With trade policy seen as unpredictable, capital expenditure decisions are being deferred. CEOs in construction and manufacturing cite the 90‑day tariff pauses and looming reviews—such as the critical minerals probe—as reasons to hold off on expansion and hiring plans. - Global Trade Outlook
The World Trade Organization recently cut its 2025 forecast for merchandise trade growth, warning that further U.S. tariffs and their spillover effects could trigger the biggest slump since the COVID‑19 pandemic .
Industry Strategies and Solutions
- Diversify Supply Chains
Building relationships with multiple suppliers across different regions helps spread risk. Firms are weighing options in countries not subject to U.S. tariffs and investing in dual‑sourcing agreements to ensure continuity. - Flexible Contracting
Incorporating escalation clauses for material costs and specifying tariff‑related adjustments in subcontractor agreements protects all parties if duties change mid‑project. - Lean Inventory and Bulk Purchasing
Companies are tightening cash‑flow management through just‑in‑time inventory, balanced with strategic bulk orders placed ahead of anticipated tariff hikes. - Advocacy and Lobbying
Industry groups like NAHB are engaging with federal agencies and Congress to seek exemptions for critical building materials, advocating for policies that boost domestic timber production and mitigate tariff harm.
Conclusion
The April 2025 tariff wave has introduced significant cost and planning challenges for the U.S. construction industry. From soaring steel, aluminum, lumber, and critical mineral prices to disrupted supply chains and project delays, stakeholders must adopt proactive strategies—diversifying suppliers, revising contracts, and engaging in advocacy—to weather the storm. While uncertainty may persist through at least 2026, informed planning and collaborative solutions can help builders, developers, and material suppliers navigate this complex landscape and continue delivering vital residential, commercial, and infrastructure projects.
Impact on the Construction Industry
- Rising Material Costs
The tariffs have led to substantial increases in the prices of key construction materials. For instance, the cost of lumber, predominantly sourced from Canada, has surged, potentially adding up to $29,000 to the price of a new home. Similarly, steel and aluminum prices have escalated, affecting the affordability and feasibility of various construction projects. - Project Delays and Budget Overruns
The sudden spike in material costs has caused delays in project timelines and budget overruns. Contractors are grappling with the challenge of absorbing these unforeseen expenses, leading to postponed or canceled projects. Fixed-price contracts are particularly vulnerable, as they may not account for such abrupt cost increases. - Supply Chain Disruptions
The tariffs have disrupted established supply chains, forcing construction firms to seek alternative suppliers or materials. This shift often results in longer lead times and additional logistical complexities, further delaying project completion and increasing costs. - Economic Uncertainty
The broader economic implications of the tariffs have introduced a climate of uncertainty within the construction industry. Fluctuating material costs and unpredictable policy changes make long-term planning difficult, discouraging investment and expansion within the sector.
Strategies for Mitigation
To navigate the challenges posed by the new tariffs, construction industry stakeholders can adopt several strategies:
- Diversify Supply Chains
Exploring alternative suppliers, including domestic sources or countries not affected by the tariffs, can help mitigate supply chain disruptions. Building relationships with a broader range of suppliers enhances resilience against future trade policy changes. - Incorporate Flexible Contract Terms
Including escalation clauses in contracts allows for adjustments in pricing to account for material cost fluctuations. This flexibility can protect both contractors and clients from unforeseen expenses due to tariff-induced price changes. - Invest in Domestic Manufacturing
Supporting and investing in domestic manufacturing capabilities can reduce reliance on imported materials. While this approach requires significant upfront investment, it can provide long-term stability and control over material costs. - Enhance Financial Planning
Implementing robust financial planning and risk management strategies can help construction firms better prepare for and respond to economic uncertainties. This includes setting aside contingency funds and regularly reviewing and adjusting budgets to reflect current market conditions.
Conclusion
The tariffs introduced in April 2025 have significantly impacted the U.S. construction industry, leading to increased costs, project delays, and economic uncertainty. By diversifying supply chains, incorporating flexible contract terms, investing in domestic manufacturing, and enhancing financial planning, construction firms can better navigate the challenges posed by these trade policies. Proactive adaptation and strategic planning are essential for sustaining growth and stability within the industry amid ongoing economic fluctuations.
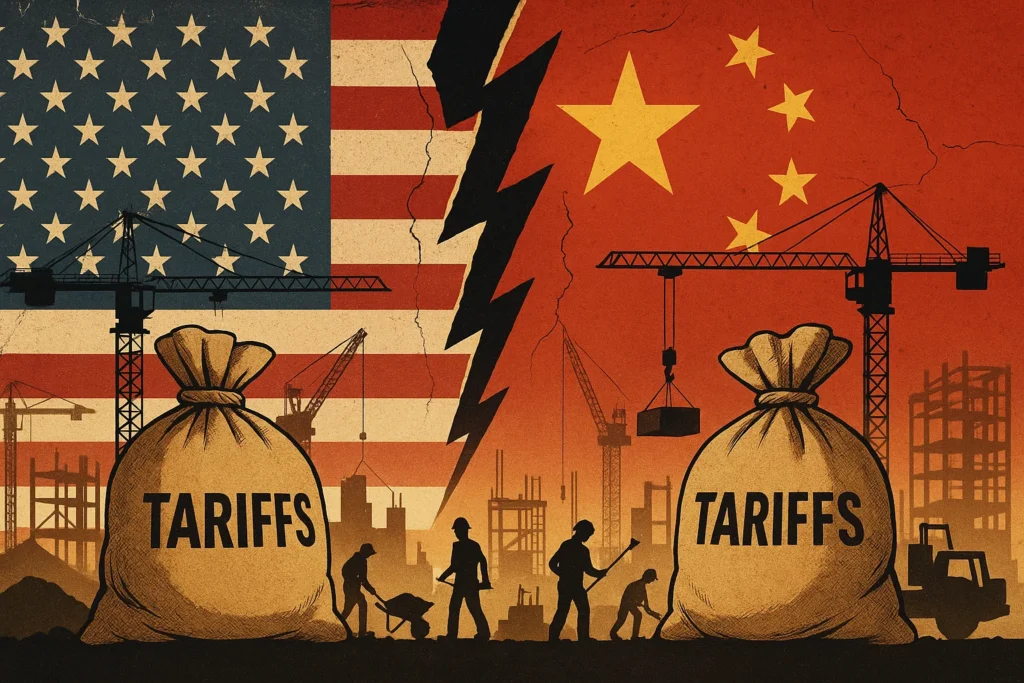